FMEA(故障モード影響度解析)とは
FMEA(Failure Mode and Effects Analysis)とは、製品や製造プロセスに潜在する故障モードを事前に洗い出し、影響を分析評価したうえで対策を講じる解析手法です。故障モードとは、故障を引き起こす不具合(原因)を指し、故障そのものを意味するわけではありません。故障モードの洗い出しにはFMEA評価フォーマット(FMEAシート)が活用されます。
なお、類似した分析手法として「FTA(Fault Tree Analysis:故障の木解析)」があります。FMEAとFTAとの違いはアプローチの仕方にあり、FMEAはボトムアップ解析、FTAはトップダウン解析です。
FMEAはさまざまな業務に適用され、大きく3つに分類できます。
工程FMEA
工程FMEA(Process FMEA:工程故障モード影響解析)とは、FMEAの考え方を製造工程管理に適用したもので、工程管理部門で利用されるのが一般的です。PFMEAまたはプロセスFMEAとも呼ばれます。製造工程に潜在する不具合を洗い出し、起こりうるミスやトラブルを予防します。製造プロセスの改善、品質保証や信頼性の向上が目的です。工程FMEAにおける故障モードの対象は、設備・人・材料・方法・計測などです。
設計FMEAと機能FMEA
設計FMEA(Design FMEA:設計故障モード影響解析)は、DFMEAまたはデザインFMEAとも呼ばれ、主に製品設計・開発部門で利用されます。製品の設計段階での故障モードを抽出し、修正などの予防処置をとるために用います。解析対象は、製品を構成する部品やユニットです。
機能FMEAは、設計FMEAの一部として実施されます。製品を構成するハードウェアやソフトウェアの機能が対象です。
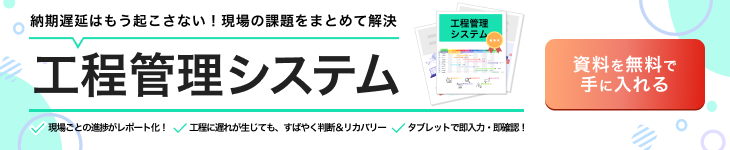
工程FMEAの重要性
製造工程で作業や設備が正常ならば、品質を保つことは難しくありません。しかし何かしらの異常が生じた場合、品質維持は著しく困難になります。
製造工程で生じるすべての異常を想定するのは容易ではありませんが、一定のパターンをもつトラブルも少なからず存在します。品質管理を徹底するためには異常事態への備えが必要であり、対策として有効なのが工程FMEAです。
例えば、新規に導入した機器特有の異常を想定するのは一筋縄ではいきません。しかし経年劣化による摩耗や断線などは想定可能です。このような不具合の原因を故障モードと呼び、故障モードの影響を考慮してトラブルを予防するのが工程FMEAの考え方です。
なお、工程FMEAで洗い出したリスクを、工程管理システムで効果的に管理することで、製品の安全性と品質を大幅に向上できます。工程管理システムは、各工程の進捗状況をリアルタイムで可視化し、ボトルネックの早期発見にも役立つため生産効率を向上させます。また、手作業によるデータ入力ミスを防止し、ヒューマンエラーの削減により、製品品質の安定化にも貢献するでしょう。以下の記事では、工程管理システムの概要について解説しているため、ぜひ参考にしてください。
工程FMEAの導入・実施方法
工程FMEAの重要性を理解したところで、具体的な導入・実施方法について理解を深めましょう。工程FMEAのおおまかな手順は以下のとおりです。
- 1.検討対象を分類する
- 2.故障モードを決定する
- 3.故障モードを分析・評価する
- 4.改善案を作成・実施する
故障モードの洗い出し方や分析の仕方について、ステップごとに詳しく解説します。
1.検討対象を分類する
作業を開始するにあたって、FMEA評価フォーマット(FMEAシート)を用意します。フォーマットの書式は特に決まっていないため、使いやすいものを準備しましょう。以下のような項目欄を設けた表を、エクセルで作成するのが一般的です。
- ●工程
- ●作業名目
- ●具体的作業
- ●想定されるミス
- ●故障モード
- ●故障による影響
- ●影響度
- ●故障の発生原因
- ●発生頻度
- ●故障の検出方法
- ●検出難易度
- ●RPN(影響度×発生頻度×検出難易度)
工程での作業を大きなくくりで分類します。「工程」と「作業名目」に、例えば「組立」「パーツ組立A」などと記入しましょう。
次に作業内の動作一つひとつを洗い出します。「具体的作業」に「部品Aを製品本体に取りつける」などと記入します。
2.故障モードを決定する
続いて「想定されるミス」「故障モード」の項目を埋めましょう。
例えば「部品の取り付けが甘い」がミス、「対象部分の接触不良」が故障モードといった具合です。分類した作業ごとに項目を記入しましょう。
大切なのは、工程のミスに起因する故障モードのみを考えることです。もし「部品Aと接合部の形が合致しない」ならばそれは設計上のミスとなり、工程FMEAにおける故障モードとはみなしません。
3.故障モードを分析・評価する
このステップでは以下の項目を考えます。
- ●故障による影響、影響度
- ●故障の発生原因、発生頻度
- ●故障の検出方法、検出難易度
- ●RPN(リスク優先度)
影響度
故障による影響度を10段階で評価しましょう。影響度は、故障による影響の大きさによって以下のように分類します。
- 10:まったく機能しない
- 9:特定の条件下で機能しない
- 8:機能しない可能性がある
- 7:特定の条件下で機能が低下する
- 6:機能が低下する可能性がある
- 5:機能はするが、改善が不可欠
- 4:機能はするが、改善すべき
- 3:影響はないと見なせる
- 2:完全に無視できる程度の影響しかない
- 1:まったく影響がない
フォーマットの「故障による影響」の項目には、具体的な影響を記入しましょう。ディスプレイがまったく機能しないような場合には、「画面が映らない」と記入します。
発生頻度
故障が発生する頻度を10段階で評価しましょう。
- 10:毎回
- 9:1日1回
- 8:1週間に1回
- 7:2週間に1回
- 6:1か月に1回
- 5:6か月に1回
- 4:1年に1回
- 3:3年に1回
- 2:5年に1回
- 1:発生しない
「故障の発生原因」の項目には、ミスを誘発する可能性がある原因を記入します。例えば「部品AとBが似ている」などが当てはまるでしょう。
検出難易度
検出難易度とは、故障やトラブルが生じた際に検出される確率のことです。検知度と表されることもあり、検出のしやすさとも捉えられるでしょう。以下のように10段階に分けられます。
- 10:検出不可
- 9:工程での検出率=10%
- 8:工程での検出率=20%
- 7:工程での検出率=30%
- 6:工程での検出率=50%
- 5:工程での検出率=70%
- 4:後の工程での検出率=100%
- 3:次の工程での検出率=100%
- 2:作業途中で検出可能
- 1:作業途中での検出率=100%
FMEA評価フォーマット(FMEAシート)の「故障の検出方法」には、具体的な検出方法を記入しましょう。「部品取り付け後、目視確認する」などが該当します。ただし人間が確認する場合、検出率は100%になりません。100%としてよいのは、機械で検出する場合のみです。
RPN(リスク優先度)
続いて、ここまで評価した影響度・発生頻度・検出難易度を掛けあわせましょう。算出された値はリスクの大きさを示す指標で、RPN(Risk Priority Number)と呼ばれます。
RPN=影響度×発生頻度×検出難易度
例えば「影響度=5」「発生頻度=2」「検出難易度=6」のとき、「RPN=5×2×6=60」となります。
4.改善案を作成・実施する
RPNをもとに、対処すべき問題に優先度付けをして、優先度の高いものから改善を目指しましょう。
改善とは、RPNを低下させることです。そのためには影響度・発生頻度・検出難易度を下げる取り組みが必要です。しかし、影響度を下げることはできないため、発生頻度もしくは検出難易度を下げるよう対策を検討します。ミスの誘発要因を取り除いたり、精度の高い検出機器を導入したりしましょう。
改善策を実施したら、再度RPNを算出して評価します。RPNが100未満になるまで繰り返しましょう。
工程FMEAを実施する際の注意点
FMEAの効果を最大化するためには、故障モードを抽出する際に網羅性と客観性が担保される必要があります。また対象のプロセスや製品によっては、評価基準の設定が異なる場合があるため注意しましょう。以下で具体的に解説します。
複数名で実施する
FMEAは、一人で行うのではなくチームを構成して複数名で実施するのがよいでしょう。一人では故障モードの抽出に抜け漏れが生じる可能性がありますが、複数人で実施すれば網羅性が高まります。故障モードに漏れがあると、異常事態が生じた場合に対応が遅れるリスクがあります。
また一人でFMEAを実施すれば、影響度・発生度・検出度を評価する場合に偏りが生じる恐れもあるでしょう。製品設計や製造、品質管理など各分野の専門知識をもつメンバーで構成すれば、多角的な視点から客観性の高い評価が得られます。
10段階の評価基準が適合するとは限らない
前出のFMEA実施方法では、故障モードの影響度・発生頻度・検出難易度を10段階に分けて評価しました。しかし、部品単体や簡単な組立設計・製造を行っている企業にとっては、段階が細かすぎるゆえに判断しにくいなどの難点があります。
企業によっては、基準を4段階や5段階に減らして評価するケースもあります。基準を減らすことで評価を選択しやすくなり、FMEA実施そのものにも時間がかからないなどのメリットがあるでしょう。
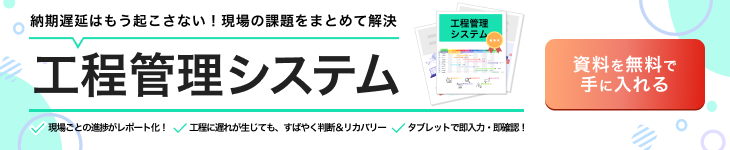
FMEAや工程管理システムを導入しリスク対策を実施しよう
工程FMEAとは、製品や製造プロセスのリスクを取り除くFMEAの考え方を、製造工程管理にとり入れたものです。故障や不具合を未然に防げるため、品質が担保され企業の信頼性向上につながるメリットがあります。工程管理システムと組み合わせることで、リスク対策の効果を最大化し、製品の品質向上を実現するでしょう。
工程管理システムは、工程進捗の可視化・作業の効率化・人的ミスの削減などさまざまなメリットをもたらします。興味のある方は、ぜひ資料請求をご活用ください。