ピッキングとは
ピッキングとは、保管されている物品を出荷する作業のことであり、主に物流の現場で使われる用語です。出荷指示が出ると該当する物品を探し出し、必要なものを集めます。そのため、商品を「ピックアップする(集める)」ことが名前の由来となっています。
目立ちにくい作業ですが、スピードや正確性が求められます。倉庫では必ず発生する業務であり、業務の効率化やコスト削減に大きな影響を与える工程です。
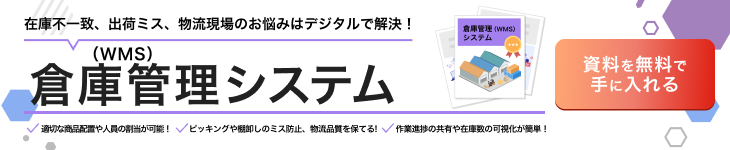
一般的なピッキング方式の種類
つづいて、一般的なピッキング方式の種類について見ていきましょう。
シングルピッキング(摘み取り方式)
シングルピッキングとは、基本的に1度の注文に対してピッキングを行う方式です。つまり、個々の顧客や出荷先ごとに必要な物品を集めて、別々に出荷をしていきます。
その都度ピッキングを行っていく方式であるため、一般的に出荷数が少ないアイテムを保管している倉庫に向いています。反対に、出荷の頻度が高いアイテムの場合だと、ピッキングのために倉庫を移動する回数が増え、効率が悪くなるでしょう。また、アイテムの種類や納品先が多い場合も有効です。
トータルピッキング(種まき方式)
トータルピッキングとは、複数の物品をまとめてピッキングする方式です。一度にまとめてピッキングした物品を荷捌き場に移し、発送先ごとに振り分けていきます。
この方式では、納品先や商品の種類が少なく、物品の数が多いときに有効です。シングルピッキングと比較すると、倉庫内を移動する回数が減り、移動距離も短くなるため効率が良いです。
しかし、荷捌きをする場所に多くの物品を一時的に保管することになり、そのスペースを確保しなければなりません。したがって、保管スペースに余裕がない倉庫では対応が難しいといえるでしょう。
ウェーブピッキング
ウェーブピッキングとは、シングルピッキングとトータルピッキングの良いところを組み合わせた方式です。トータルピッキングの仕組みを細かく分け、シングルピッキングを複数同時に行うことで効率化を図ります。
この方式を採用すると、商品の総量・種類が多い倉庫でも、断続的に作業が可能です。しかし、効率良く作業を進めるためには、ピッキングする総量を把握し、ピッキングの処理順番を的確に決めなければなりません。そのため、後述するWMS(倉庫管理システム)などを採用した倉庫で使われることが多いです。
ITを活用したピッキング方法の種類
通常のピッキングは、出荷指示書に記載されている物品と数量を確認し、保管スペースから商品を探し出します。しかし、手作業だと正確性が低くミスが発生しやすいため、近年ではITを活用したピッキングが主流となっています。
そこで、ITを活用したピッキング方法の種類にはどのようなものがあるのか見ていきましょう。
バーコード・QRコード
バーコード・QRコード方式は、物品にバーコードやQRコードを貼り付け、専用のスキャナで読み込む方法です。出荷指示書に記載されている情報と異なる物品を読み込むとエラーが表示されるため、目視で確認するよりも正確です。
比較的簡単に導入できるため、現在バーコードやQRコードを使ったピッキングを行っている企業は多くいます。
RFID
RFIDとは「Radio Frequency Identifier」の略であり、タグを使ったピッキング方法です。専用の無線通信を行う機械を使ってRFIDタグの情報を読み込むため、バーコード方式と同様にミスなく正確にピッキングを行えます。
バーコード方式よりも情報を読み取る範囲が広く、効率良く出荷する商品をピックアップできます。
デジタルピッキング(DPS)
DPSとは、商品を保管している棚にデジタル表示器を取り付ける方法です。その表示器のランプにより、商品の場所が分かる仕組みとなっています。
この方法であれば専用のハンディ端末が必要なく、初めて倉庫で作業をする人でも物品の保管場所の把握が可能です。商品知識がない人でもピッキング作業ができるだけでなく、作業スピードの向上や出荷指示書の削減も期待できます。
特に多くの人が働く大型の倉庫では、新人への教育時間を大幅に短縮できるため活用されることが増えています。
ピッキング作業を効率化するためのポイント
最後に、ピッキング作業を効率化するためのポイントを見ていきましょう。
作業動線を短縮する
人間が行う以上、ピッキング作業の移動時間・距離を短縮する必要があります。もし倉庫内に商品が乱雑に保管されていれば、倉庫内を歩き回らなければなりません。そのため、在庫保管場所の最適化を図り、作業動線を短縮する必要があります。
例えば、商品の出荷頻度を分析して、頻度が高いものを出荷作業を行うエリアの近くに保管するようにしましょう。棚の取り出しやすい位置に配置するのも効果的です。
DPSを導入している高度にシステム化された倉庫であれば、出荷指示に従えば最短距離で物品をピッキングできるため効率が良いです。
作業を標準化・マニュアル化する
ピッキング作業にかかる時間や効率は、その作業を行う従業員のやり方やスキルに依存する部分が大きいです。例えば、ベテランの作業員と新人の作業員であればピッキングにかかる時間は大きく変わるでしょう。
そこで、作業員それぞれのやり方ではなく、効率が良い作業方法を標準化・マニュアル化するのが有効です。作業方法を統一すると、経験が少ない作業員でもスムーズにピッキングでき、全体の作業効率が向上します。
すでにマニュアルを使って運用している場合でも、経験がある従業員の意見を取り入れて見直すのがおすすめです。
WMS(倉庫管理システム)を活用する
WMS(倉庫管理システム)とは、倉庫の在庫情報・入庫情報・出荷情報などを一元管理できるシステムです。バーコードやRFIDタグ、DPSとの連携により、ピッキングミスを減らすだけでなく、在庫のカウントも自動で行えます。
このようにシステム化することで、在庫の最適化を図れるだけでなくピッキングの効率も高くなるでしょう。従業員の作業品質を統一すれば、今まで正社員が行っていた作業がアルバイトやパートでも行えます。
新人を教育するコストを削減可能なだけでなく、作業効率を高められれば少ない人員で稼働できるため、人件費の削減にも繋がります。在庫管理やピッキング作業の正確さが増せば、イレギュラーな対応に追われることも減り、物流の品質も向上するでしょう。
WMS(倉庫管理システム)については、以下の記事を参考にしてください。
最適なピッキング方式を選択し、作業を効率化しよう
倉庫内業務の効率を高めるには、ピッキング作業の改善が有効です。
ピッキングには、シングルピッキングとトータルピッキングがあり、適した手法は倉庫のスペースや商品の種類、頻度によって変わります。IT化を進めれば両者のメリットを採用したウェーブピッキングを実践できます。
WMS(倉庫管理システム)を導入すると在庫管理やピッキング作業の最適化が可能です。最適なピッキング方式を選択して作業を効率化しましょう。
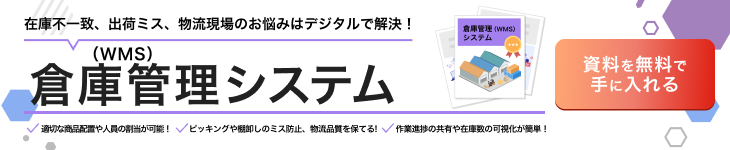