適切な倉庫レイアウトの効果
近年、EC市場の需要が高まり物流は拡大しています。倉庫の機能性を高め、効率的に活用するためには、倉庫レイアウトの最適化が必要です。無駄のないレイアウトは、コスト削減・業務効率化に有効だからです。
倉庫レイアウトが適切でない場合に生じるデメリット、最適化された場合のメリットは、以下のとおりです。
- ■倉庫レイアウトが不適切(商品が整理整頓されずに乱雑に保管)な場合
- →最短ルートで商品をピッキングできないため、作業時間が増え人件費も増加。
→倉庫を借りている場合、スペースを有効活用できずに保管費が余分に発生。
- ■倉庫レイアウトを改善(最適化)した場合
- →移動距離を短縮できて作業効率が向上。
→人件費や管理費などのコスト削減。
→商品の取り違えなどのリスクを低減。
倉庫レイアウトの設計は、できるだけ倉庫を新設したタイミングで実施するのがおすすめです。すでに倉庫をもっており、レイアウトの大幅な改善を行う際には、レイアウトの考え方や設計方法を理解したうえで、実行しましょう。なお倉庫内の保管量や商品の種類などの状況によって適したレイアウトは変わります。そのため、こまめな見直しや改善が必要です。
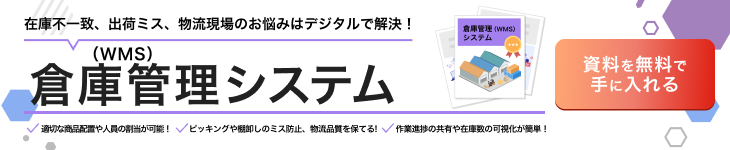
倉庫の基本レイアウト
倉庫の基本レイアウトは、主にI型とU型です。
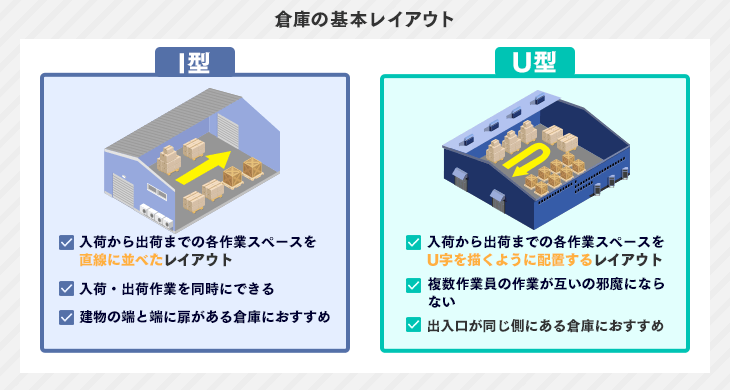
I型のレイアウトは、入荷から出荷までの各作業スペースをまっすぐ順番に並べます。作業スペースが狭いにもかかわらず商品量が多い場合に有効で、入荷・出荷作業を同時にできる点が大きなメリットです。建物の端と端に扉があり、入荷と出荷の場所を別々にできる倉庫に向いています。しかし、狭い作業スペース・通路で複数の作業員が同時に仕事をすると互いの作業の邪魔になるため注意が必要です。
U型のレイアウトは、入荷と出荷場所が同じ側にあり、Uを描くように配置します。各作業を流れるように行うため、複数の作業員が仕事をしても互いの邪魔になりません。倉庫や通路が狭い場合でも効率よく作業できます。しかし保管スペースを確保した場合、作業スペースが狭くなるため注意してください。
倉庫のレイアウトは一筆書きできる作業導線が理想といわれています。倉庫内を行き来せずに作業できるよう、それぞれの作業スペースを配置することが重要です。
倉庫レイアウトの設計方法
倉庫レイアウトの設計手順について確認しましょう。
1.入荷~出荷までの作業工程を確認する
まずは現状の作業工程を洗い出します。作業工程全体の確認により、確保・共有すべきスペースを決められます。また倉庫によって詳細は異なりますが、倉庫内の主な作業工程はある程度決まっているのが一般的です。
- 倉庫内の主な作業工程
- 1.入荷
- 2.検品
- 3.入庫
- 4.保管
- 5.出庫
- 6.梱包
- 7.出荷
倉庫内で実施する作業を明らかにしたうえで、各作業に要するスペースを検討しましょう。
2.倉庫全体のレイアウトを決める
倉庫全体のスペースを確認して、デッドスペースが生まれないようにレイアウトを決めます。このとき、「平面ロス」だけでなく、「高さロス」が生じないように意識しましょう。
■平面ロス……スペースがあるのに商品が置かれていないことによるロス
■高さロス……倉庫の高さを有効活用できていないことによるロス
例えば重量ラック間に棚を設置し、通路の上部に保管スペースを構築するなどが挙げられます。
また各工程から次の工程に進むとき、作業場所が遠いと移動時間が無駄になります。作業をする場所も考慮しながら導線を確認し、効率がよい最適なレイアウトを設計しましょう。
3.在庫品の保管場所を決める
商品の出入りが激しいものを重点的に配置決めします。例えば重要度の高い商品は中央通路寄りに配置、一方重要度の低い商品は台車が通れないような通路幅の狭い通路に配置するなどします。可能な限り無駄のない動きでピッキングできるレイアウトを作成しましょう。
倉庫内の商品を適切にレイアウトするには
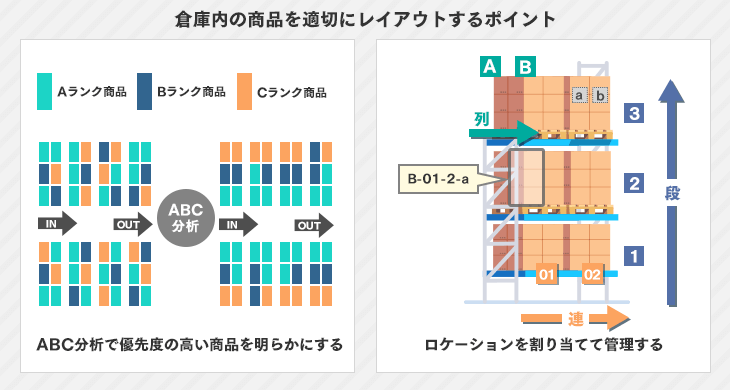
同じ作業スペース内で、どこにどの商品を配置するかでも作業効率は変わります。例えばよく利用するものは取り出しやすい位置に、使用頻度が低いものは奥に配置すると無駄な動きを減らせます。つまり出庫頻度に応じた商品レイアウトが必要です。ここからは商品のレイアウトにおける考え方やコツを紹介します。
ABC分析で優先度の高い商品を明らかにする
ABC分析とは重視度別に商品をグループ分けする方法です。今回は「出荷頻度」によって商品を分類します。
- Aグループ
- 流動性・出荷頻度が高い。頻繁に商品を取り出すため、作業効率を優先する。
- Bグループ
- 流動性・出荷頻度が平均的。作業効率と保管効率のバランスを考えて保管する。
- Cグループ
- 流動性・出荷頻度が低い。商品を取り出す回数が少ないため、状態が悪くならないように保管効率を優先する。
優先度の高いAグループの商品を、出入り口付近やメイン通路から最短距離の導線付近に集中させればピッキング効率があがります。
ロケーションを割り当てて管理する
ロケーションとは商品の保管場所を示す番号のことで、商品の住所のような役割をもちます。棚で管理している場合、1段ずつにロケーションを割り当てます。棚の番号で商品の位置がすぐにわかるのが利点です。
保管効率を計測する必要性
レイアウトを決めたうえで商品を保管しても、運用を続けていけば状況は変わってくるでしょう。倉庫のレイアウトが最適かどうかは、保管効率を算出して判断します。保管効率は以下の公式で算出します。
保管効率=保管物の容積÷保管エリアの容積
保管効率の値が高ければ、少ないスペースにより多くの商品を保管できているといえます。保管効率の値が小さくなれば、改善の余地があるでしょう。レイアウトの見直しが急務です。保管効率を高めるためには、倉庫を平面的ではなく立体的に活用することも重要です。また、各棚に無駄なスペースがあると保管効率は下がるため、注意しましょう。
倉庫レイアウトの設計方法を知って作業効率を上げましょう
倉庫の作業効率や保管効率を高めるためには、レイアウトの最適化が必要です。
最適なレイアウトで商品を保管できればコスト削減にもつながります。レイアウトは頻繁に変更することが難しいため、慎重に決めましょう。 倉庫のレイアウトを設計するときは、まず全体のレイアウトを決め、ABC分析を活用して在庫品の保管場所を決定してください。
保管効率を算出し定期的に倉庫レイアウトの改善に努めましょう。
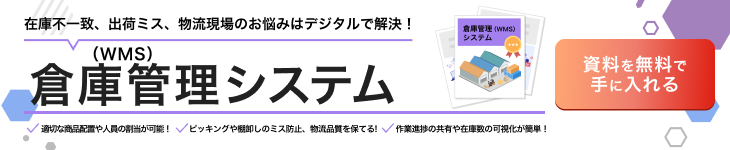