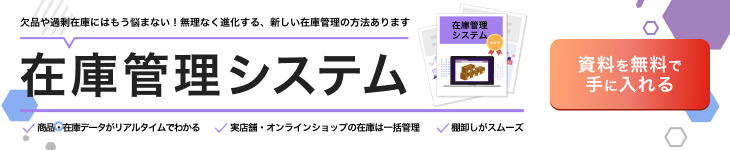
6種類の発注方式
在庫管理をするうえで発注は重要です。定期的に発注し、在庫がなくならないようにする必要があります。発注方式には以下の6種類があります。
- 1.定量発注方式
- 2.定期発注方式
- 3.簡易発注方式
- 4.不定量不定期発注方式
- 5.同期化発注方式
- 6.分納発注方式
各々の方式について、詳しくみていきましょう。
1.定量発注方式
残りの在庫が一定数(発注点)以下になったら発注する方式です。急な需要の増加に対応しづらいため、基本的には安定した出荷量の商品に向いています。
2.定期発注方式
「毎月1日」といった形で発注するタイミングを設定する方式です。需要の増減に柔軟に対応できますが、毎回発注量を決めるのが手間になる恐れもあります。
3.簡易発注方式
重要度の低い商品に適用される方法です。「ダブルビン方式」と「補充方式」に大別されます。
ダブルビン方式
ダブルビン方式はAとBの2つの箱があることを前提とします。まずはAから使い始め、Aが空になったら初めてBを開封し、新たに1つ発注する方式です。
「空になる」という作業者が視覚的に捉えやすい状態を発注のタイミングとするため、分かりやすいという特徴があります。
補充方式
補充方式は、一定量を使用したらその分だけ発注する方式です。商品ごとに一定量とはどのくらいなのか、過去の出荷データを元に簡易的に決めておきましょう。出荷頻度は少ないけれど、欠品時の損失が大きくなる恐れのある商品に適用するのがおすすめです。
4.不定量不定期発注方式
発注点を下回ったときに発注するのは定量発注方式と同じですが、発注量はその都度需要に応じて決める方式です。発注数ではなく、出荷対応日数やリードタイム日数、在庫日数を元に毎回異なる数を発注します。
5.同期化発注方式
発注先と契約し、毎日一定数を納品させる方式です。急な需要の変動が起こった場合は対応しきれないこともありますが、欠品しても問題ない商品の場合は毎回発注する手間を省けるため、有効な発注方式と言えるでしょう。
6.分納発注方式
定期的に在庫数と計画を確認し、その計画に合わせて在庫が必要になるタイミングで発注する方式です。いつ、何が、どのくらい必要かは、年間スケジュールを元にある程度決まっていますが、予定は常に変わっていくものです。その都度計画の変更に対応しながら発注していきましょう。
定量発注方式と定期発注方式の違い
6つの方式の中で最も一般的なのが、定量発注方式と定期発注方式の2つです。この2つの違いは、「ある在庫量を下回ったら決められた量を発注する」か「定期的に必要に応じた在庫を発注する」かという点です。
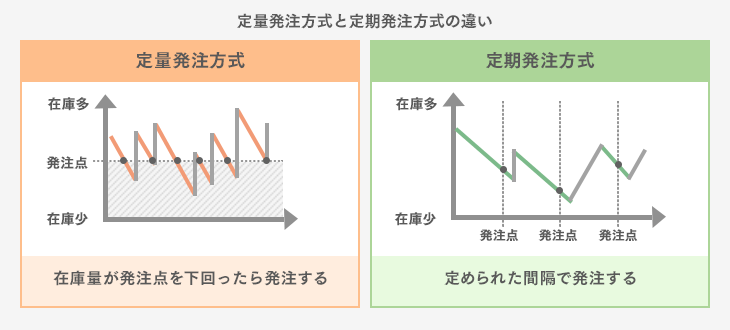
では、それぞれについて詳しく解説します。
定量発注方式とは
定量発注方式では商品ごとに決めた発注点を下回った際に新たにその商品を発注します。発注点とは「その数量を下回ったら新たに発注すると予め決めた数値」のことです。
発注点を決めるための計算式は以下の通りです。
「発注点=(1日の在庫消費量×調達期間)+安全在庫量」
発注してから商品が届き、在庫数が増えるまでの間に消費される在庫は残しておく必要があります。安全在庫は急に大量の出荷が必要になった際の需要の変動を緩和する役割を果たします。
定量発注方式の具体例
例えば、Aという商品の発注点を5とします。毎日出荷作業をし、ある日ピッキング時に残りの在庫数が4になりました。これはAの発注点を下回ったことになるので、新たにAを発注し在庫数を増やしておく必要があります。
定量発注方式のメリット・デメリット
定量発注方式のメリットは発注する量が毎回同じで手間がかからない点であり、デメリットは安全在庫を考慮してはいるものの基本的に需要の変動が少ないものにしか適用できない点です。主に、在庫管理においてはやや優先度の落ちる、ABC分析(後述)でBグループに分類される商品が対象となります。
定期発注方式とは
定期発注方式とは、1週間に1度や1ヶ月に1度など予め決めておいた発注間隔で必ず発注を行うことです。発注量はその都度在庫状況を確認したうえで決めるため、毎回異なる量となります。
発注量を決めるための計算式は以下の通りです。
「発注量=(発注間隔+調達期間)× 使用予定量 + 安全在庫 - 現在の在庫量 - 現在の発注残」
発注間隔(次回発注するまでの期間)と調達期間(発注してから商品が届くまでの期間)の合計に出荷予定の量をかけたものを求めます。そしてその数値から、現在手元にある在庫とすでに発注して届く予定になっている量を差し引いたものが発注量となります。
定期発注方式の具体例
例えば、Bという商品は発注間隔を月に1度と定められています。今月在庫数を確認したところ、在庫数がかなり減っていたため10個発注を行いました。翌月再び在庫数を確認すると、先月からほとんど在庫数が減っていなかったため、3個のみ発注することになります。
定期発注方式のメリット・デメリット
定期発注方式は、毎回発注量を決めることで需要の変動が大きい商品にも適用可能である点がメリットですが、手間がかかる点はデメリットと言えるでしょう。主に、在庫管理においては優先度の高い、ABC分析でAグループに分類される商品が対象となります。
定量発注方式と定期発注方式、どちらが最適?
定量発注方式と定期発注方式はどちらも一長一短であり、どちらかが優れているわけではありません。どちらの発注方式を採用するかは、ABC分析でその商品の売上が全体の売上に占める割合が大きいか小さいかで決めると良いでしょう。
Aグループに分類される商品は全体の売上を支える花形商品です。万が一欠品した場合に売上全体への影響が大きいため、発注のたびに発注量の調整が利く定期発注方式を採用すべきです。毎回発注量を決める手間をかけたとしても、その分の売上が見込めるでしょう。
一方、Bグループ商品については全体の売上高への影響がそこまで大きくないため、いかに手間をかけずに省力化した発注をするかが重要です。Aグループ商品に比べて出荷頻度も低いため、発注点を下回ってから初めて発注をかけても欠品しづらいでしょう。
それぞれの商品の出荷の傾向を把握して、最適な発注方式を選びましょう。
適切に在庫管理を行うためのポイント
適切に在庫管理を行うためにはいくつかのポイントがあります。
管理する在庫の優先度を決める
すべての在庫を平等に管理するとなると負担は大きくなります。そのため、管理する在庫の優先度を決めましょう。
ABC分析を行い、以下の3種類に分類しましょう。
- A:売上の7割を占める商品
- B:売上の1~3割を占める商品
- C:残りの商品
前述した通り、Aは定期発注方式、Bは定量発注方式が向いています。負担が大きい発注方式は重要度の高い商品に行い、重要度の低い商品は手間を減らすことで効率的に発注業務を行うのがポイントです。
ABC分析について詳しく知りたい方は、こちらの記事をチェックしてみてください。
無駄な在庫を持たないようにする
無駄な在庫をできるだけ省くため、以下のことに注意しましょう。
生産リードタイムを短縮する
生産リードタイムとは、原料を投入してから製品が完成するまでの期間です。これが長いと仕掛品を多く抱えることになり、在庫が膨らみます。
他にも発注してから納品されるまでの納入リードタイムや物流にかかる物流リードタイムがあります。ただし、これらは自社の努力だけで改善するのが困難です。そのため、まずは生産リードタイムの短縮に着手しましょう。
需要の予測をする
需要を予測できれば無駄な在庫を抱える必要がなくなります。予測される需要に応じて発注量を増減させることができます。
しかし、需要予測は確実に当たるものではありません。そのため何度か予測を試みて、実際の結果と照らし合わせてその誤差を確認しましょう。その誤差も踏まえたうえで予測した量を発注すれば、無駄を省きつつ余裕のある発注ができます。
発注方式の違いを理解して適切な在庫管理をしよう
在庫管理において重要な「発注方式の違い」について解説しました。業種によって適した発注方式が異なりますので、在庫管理がうまく行かないという場合は、今一度自社の発注方式を見直してみてください。在庫管理システムの導入を検討してみることも業務効率化のカギとなるでしょう。
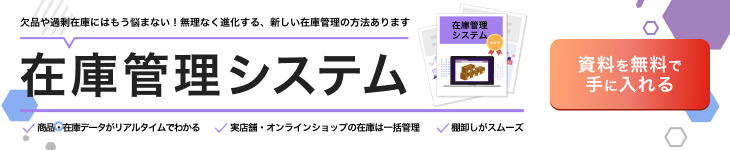