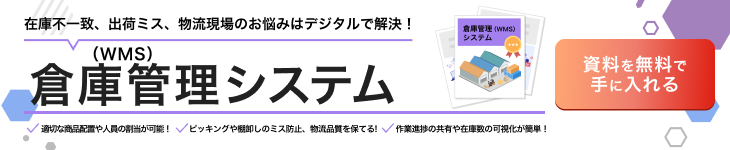
倉庫における出荷作業の工程
倉庫における出荷作業は、どのような工程で行われるのでしょうか。
ピッキング
倉庫の棚から目的の商品を取り出す作業です。企業によりさまざまな種類の荷物を扱います。重いものを取り出す際は、フォークリフトや台車が必要です。
ピッキングの方法は、「摘み取り式」と「種まき式」が知られています。摘み取り式は、倉庫内を移動して商品を一つ一つ取り出していく方式です。種まき式は倉庫内を移動せずに、ベルトコンベアに流れてくる商品を取り出します。どちらか一方だけでなく、両方の方式を採用しているところも多いです。
検品
製造業や物流業などで、商品に問題がないかを確認する作業です。食料品であれば鮮度や損傷具合、衣料品であればほつれやよれ具合などを確認します。製造業の場合は、取り扱い商品がさまざまなため、検品項目も複雑になりがちです。
物流業は、納品書や伝票に書かれている数量と、実際に保管されている在庫量を確認するのがメインとなります。
梱包
倉庫内に保管されている商品を、お客さんに届けられる状態にする工程です。配送中に商品が壊れないように内装や外装を固定します。中には、検品や仕分け業務の一部を行うところもあります。梱包材の種類は、外装・内装に分かれています。
一般的な梱包材は、以下のとおりです。
- 外装
- ダンボール、木箱、スチール箱
- 内装
- 発泡クッション、エアパッキン、新聞紙、ラップ
ダンボールはもっとも一般的な梱包材で、コストが安く強度もあります。しかし水に弱いため、雨の日の配送には向きません。木箱は段ボールより高価ですが、強度と防水性に優れています。商品の形状に応じて加工できるのも特徴です。一番強度があるのがスチール箱で、繰り返し使えるほどの耐久性があります。
内装は、衝撃を吸収できれば何でもよいというのが通説です。梱包作業が終わると、トラックの荷台に商品を積み込みます。
出荷作業の改善フロー
出荷作業を改善するには、どのような段階を踏めばよいのでしょうか。
1.現状の把握
まずは、作業に関わる全ての人が目的を共有し、現状の課題点を把握することが大切です。現状を把握できれば、何から手をつければよいかが明らかになります。最初は大まかでもよいので、出荷作業を工程別に分けましょう。「ピッキング」「検品」「梱包」「積込」などのように、ざっくりとした分類でもかまいません。
次に工程別の作業時間を把握します。毎日作業者に、15分ごとでもよいので、どの作業をしていたかを報告してもらいましょう。作業工程と時間を紙に書いて提出する形式を取るのがおすすめです。
管理者はデータを収集し、一人当たりの生産性「MH」を計算します。例えば1時間に100個の荷物をピッキングする作業者は、MH100などと表すとよいでしょう。その日の出荷作業量を、MH・作業時間・作業人数をかけたもので割ると、その日必要な作業員数を算出できます。
このようにMHは、人員や作業スケジュールの策定にも有効です。
2.施策の選定・実施
現状の課題を把握したら、その問題点を改善できるような施策を選定し、実施することが大切です。
作業マニュアルの作成
効果的な施策を策定しても、作業員それぞれが独自のやり方をすると、全体の効率が下がります。そのため、作業マニュアルを作成して、どのような社員でも同じように作業できるようにすることが重要です。
属人化を避けることで、アルバイトや派遣社員などにもベテラン社員と同等の活躍が期待できます。
出荷作業を効率化するシステムの導入
システムを導入すると、出荷作業が効率化されます。
例えばデジタルピッキングシステムは、目的の商品がある場所に取り付けられた表示器のランプが点灯する仕組みを搭載しています。これを活用すると、商品を探し出すまでの時間を短縮するだけでなく、ミスを減らすことも可能です。
また、ハンディターミナルと連携できる在庫管理システムを導入した場合、画面上だけで在庫管理が可能です。梱包の場合は、梱包機や帯掛機を用いれば、仕上がりもきれいになります。システムにより業務が効率化されると、余剰労働力を別業務に回せます。これは事業規模の拡大につながるため、利益の向上にも効果的です。
WMS(倉庫管理システム)であれば、在庫に限らず倉庫内の人員配置や設備の管理も行えるので、導入を検討してみてください。
3.効果測定・仕組化
施策後の効果を検証し、その施策を継続するかを決定します。
手戻り時間・損失額・コストがどれくらい減っているのかなどをグラフ化し、定量的に分析しましょう。こうすると実施前の課題点が改善されたか確認しやすく、具体性が高まり、より詳細な検証が可能です。
その施策が役立つものであれば継続的に仕組み化し、効果のないものならさらなる改善案を模索します。改善案の選定方法は、よく話し合ってから優先順位を決めましょう。施策の効果は、掲示板などを利用して関係者全員に周知します。
システムを導入し出荷作業が改善した事例
ある企業では出荷作業を人の手で行なっていたため、月に数回ほどミスが発生していました。トラブルのたびに、代替品の発送・伝票整理・返品処理などが増えたため、無駄なコストも増大していたそうです。そのため出荷ミスをなくし、無駄な作業を減らす必要がありました。
システム導入後は、高精度な在庫管理が可能になり、誤出荷がなくなりました。バーコードリーダーを利用するようになったため、作業者の負担も軽減されています。
出荷作業を改善して、倉庫作業の効率化を図りましょう
倉庫内の出荷作業は、ピッキング・検品・梱包などの工程があります。
業務を効率化させたい時は、それぞれを工程別に分類し、現状把握を経て、改善案を盛り込んだ施策を策定・実行しましょう。実施後は、施策の効果を検証・分析し、継続するかどうかを決めます。効率的に改善させたい場合は、システムを導入するのがおすすめです。出荷作業を見直して、自社の倉庫業務を効率化させましょう。
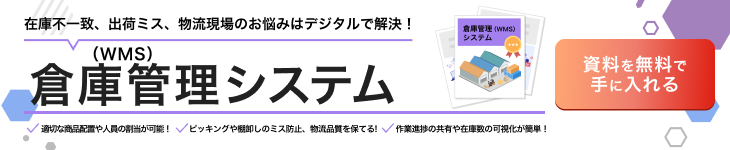