WMS(倉庫管理システム)と現場のギャップを埋める方法
WMSは入荷・出荷などの倉庫内の現場作業をリアルタイムで可視化し、効率化できることをメリットとしています。
そのため、現場での実際の作業状況をWMSで正しく把握できるようにすることが重要です。実際の作業状況とWMSから確認できる作業状況にギャップがあるようでは、導入の意味がありません。
WMSを最大限活かすために、現場とWMS双方の視点から見直しを行いましょう。
現場の作業をWMSに合わせる
まずは現場作業を可能な限りWMSに合わせることを検討しましょう。WMS製品は多くの導入成功事例をベースに、ベストプラクティス(最も効率の良い方法)を実現できるように作られています。
現場作業の手順は企業や倉庫ごとにローカルルール化しがちですが、WMS導入をきっかけにベストプラクティスに近づけるべく、作業を標準化する絶好の機会と言えます。作業フローをマニュアル化して、現場の作業手順を統一していきましょう。
また在庫の破損、紛失、持ち出しなどの例外的な動きについても、対応手順を洗い出して必ずマニュアル化するようにしてください。作業の標準化は現場の協力が必要かつ工数がかかる作業ですが、WMS導入には欠かせない工程のためしっかりと取り組みましょう。
WMSを現場の作業に合わせる
現場作業をWMSに合わせるばかりでは、スタッフから反発があったり、どうしてもWMSに合わせるには難しい部分も出てきます。例えば、WMSが多機能過ぎて使いづらい、WMSの操作性に問題がありミスが起きるなどの状況が考えられます。
使用する機能を制限する
多機能過ぎて使いづらいと感じる場合は、使用する機能を制限するのが良いでしょう。WMS選定に関わる情報システム部門はよかれと思って多機能なWMSを選びがちです。
しかし今すぐに使う予定のない不要な機能も多く、必要な機能についてもいきなりすべての機能を使いこなすのは困難です。+αの便利な機能については、少しずつ機能を開放していき慣れていくようにしましょう。
カスタマイズで操作性を改善する
導入後、いつまでも操作ミスが減らないのであれば、操作性に問題がある可能性があります。
その場合は使いやすくカスタマイズすることも視野に入れましょう。現場担当者に操作性に問題がある箇所を確認することで、間違いやすいボタンの配置、機能の名称、入力するボックスの順序など、改善できる箇所が見つかるかもしれません。
現場の声を聞きコストの許す限り、要望を取り入れましょう。
リアルタイムにデータ入力できているか確認する
WMS上の理論在庫と倉庫の実在庫にタイムラグが生じることがあります。その原因の多くは現場での入力の遅れにあります。入力を後回しにし手の空いたときにWMSに入力することが、在庫数の合わなくなる原因になります。
倉庫管理は物流システムなどとの連携が求められるため、リアルタイムに反映されないと、倉庫管理の前後のシステムに影響を与えることになります。納期遅れなどのトラブルは、お客様からの信頼を失いかねません。
WMS導入直後は作業方法に不慣れであったり、毎回入力するのが手間と感じることもありますが、ハンディターミナルの活用やRFIDの導入を検討しながら、リアルタイムなデータ入力を徹底しましょう。
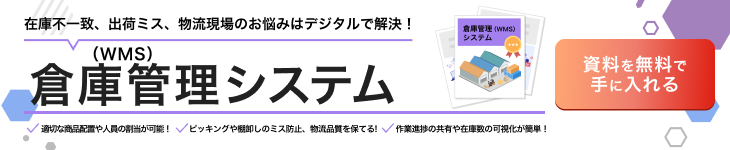
WMS(倉庫管理システム)と既存システムの連携を図る
WMS自体は問題なく稼働しているものの「現場作業の省力化や在庫の見える化がうまくできない」「思っていたような効果が得られない」という話がよく聞かれます。これらの原因の多くはWMSと前後のシステム連携がうまく機能していないことが考えられます。
WMSは受発注システムや在庫管理システムなど、一連のSCM(サプライチェーンマネジメント)を構成するシステムの1つです。単独のシステムとして稼働しているのでは、大きな効果を期待できません。
前後のシステムとの連携を考える際は、SI事業者(システムインテグレータ:システム構築サービス事業者)と協力しながら作業を進めましょう。自社のみで現状分析~構築まで行うのは難しいため、SI事業者の力を借りることでよりスムーズに進めることができます。
連携時は一時的にシステムの稼働を停止する必要も出てくるため、WMS導入後に慌てないよう、事前に関係部門と調整をして計画的に実施しましょう。
WMS(倉庫管理システム)導入後も改善を続けよう
WMS導入には高額な費用と多大な工数がかかっています。導入後すぐに効果が得られないと焦るものですが、どこに問題があるのか現状把握をし、一つずつ解決していくことで必ず導入したことによる効果を得ることができます。
自社のみで対処するのが難しい場合は、WMSを提供したベンダーを頼るのも一つの方法です。WMSを最大限活用し、自社の倉庫業務を改善しましょう。
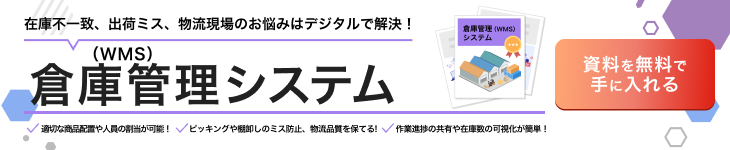