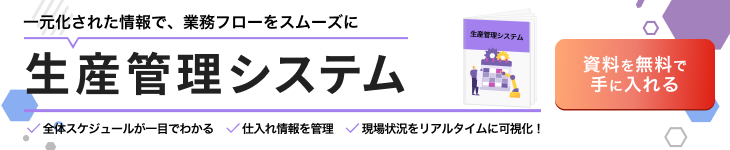
生産管理でよくある課題
生産管理は、企業にとって重要な業務の一つです。しかし、煩雑な業務が多く、生産管理に課題を抱える企業は少なくありません。ここでは、生産管理業務でよくある課題を紹介します。
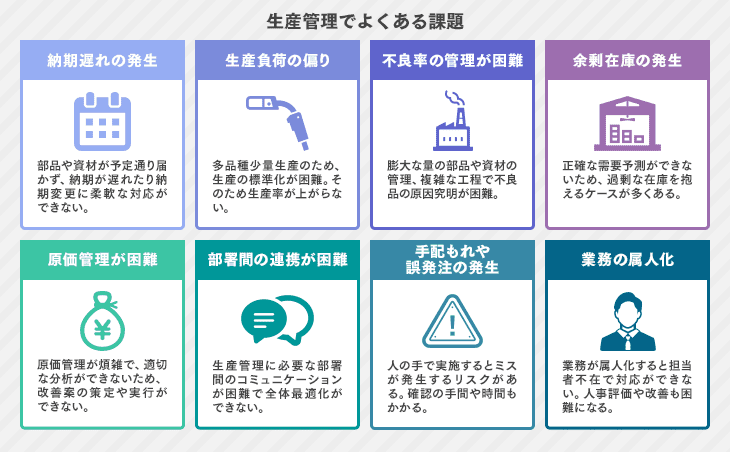
- ■納期管理と生産効率
-
- 納期遅れの多発:部品や資材の納入遅延により、完成品の納期遅れや納期変更への柔軟な対応が困難になります。
- 生産負荷の偏り:多品種少量生産の傾向により、生産の標準化や平準化が難しくなっています。
- ■品質と在庫管理
-
- 不良率の管理:複雑な生産工程や膨大な部品数により、不良率の原因究明が困難です。
- 過剰在庫の発生:需要予測の難しさから、過剰在庫を抱えるケースが多く見られます。
- ■コスト管理と情報連携
-
- 原価管理の困難さ:複数の部品や資材を扱うため、正確な原価管理と適切な分析が難しくなっています。
- 部署間の連携不足:各部署の独立した目標設定により、全体最適化を実現できないことがあります。
- ■人的要因と業務の効率化
-
- 手配漏れや誤発注:人が関わる工程では、ミスのリスクを完全になくすことが難しく、多重チェックによる時間的ロスが発生します。
- 業務の属人化:特定の担当者にしかわからない業務が増え、柔軟な人員配置や業務改善が困難になっています。
これらは多くの企業が直面している課題ですが、適切な対策を講じることで改善が可能です。
生産管理業務における課題解決には、生産管理システムがおすすめです。次のボタンからおすすめ生産管理システムの資料請求(無料)ができるので、ぜひご覧ください。
生産管理の課題を解決する方法
生産管理において多くの企業がさまざまな課題や悩みを抱えています。ここでは、課題解決方法を紹介します。
進捗状況の可視化
生産現場では、さまざまな工程があります。担当者でないと、現在どのような状況なのかがわかりません。生産活動のすべての進捗を可視化すれば、課題点の把握ができます。どこの工程が原因で遅れているのか、生産性が低いのかなどを把握することで、具体的な改善策の実行が可能です。
業務のマニュアル化
業務の属人化が進むと、担当者不在時に対応ができません。また、異動や退職により引き継ぐ場合も時間を要します。作業内容をマニュアル化すれば、担当者以外の対応が可能になります。また、業務内容が可視化されると改善策も提案しやすいでしょう。
生産管理システムの導入
生産管理システムとは、生産管理で必要な情報を一元管理するためのシステムです。工程管理や在庫管理、品質管理などの業務を効率化できます。生産管理におけるさまざまな情報が可視化されることで、適切な生産計画が立てられまする。
生産管理システムには、業務の課題解決につながる機能が多くあります。生産管理システムで実施できる代表的な内容は、以下のとおりです。
- ●材料調達の最適化
- ●生産負荷の平準化
- ●不良品の発生原因の特定
- ●正確な在庫管理
- ●正確な原価管理
- ●生産情報の共有
- ●生産情報の一元管理
ほかにも、生産方式などにあわせた製品があります。以下のボタンより最新の資料請求ランキングを確認できるので、生産管理システムの人気傾向が知りたい方はご覧ください。
生産管理システムによって解決できる課題
上述のとおり、生産管理システムの導入は、多くの企業が抱える生産管理の課題を効果的に解決する手段となります。次に、生産管理システムによって解決できる主な課題とその解決方法を説明します。
- ■納期管理の改善
- 生産管理システムは、リアルタイムで生産進捗を把握し、納期遅れのリスクを早期に特定します。また、生産スケジュールの最適化機能により、納期順守率に大幅な向上が可能です。
- ■生産効率の向上
- システムによる生産計画の最適化により、設備稼働率を向上させ、生産負荷の平準化を実現します。これにより、多品種少量生産にも柔軟に対応できるようになります。
- ■品質管理の強化
- 生産管理システムであれば、不良品発生の傾向分析や、工程ごとの品質データの収集・分析も可能です。品質問題の早期発見と迅速な対応によって、全体的な品質向上につながります。
- ■在庫の最適化
- 需要予測機能と連携した在庫管理により、過剰在庫や欠品を防ぎます。適正在庫の維持が可能となり、在庫コストの削減と同時に、必要な材料・部品の確保を実現します。
- ■原価管理の精緻化
- 製品ごとの詳細な原価計算が可能となり、正確なコスト把握と分析ができるようになります。これにより、収益性の改善や競争力の強化につながります。
- ■部門間連携の強化
- システム上で各部門の情報を一元管理することで、部門間の情報共有がスムーズになります。全社的な最適化が図れ、意思決定の迅速化にもつながります。
- ■ヒューマンエラーの低減
- 手作業での入力や管理を最小限に抑えることで、手配漏れや誤発注などのヒューマンエラーを大幅に減少させます。自動化された発注システムにより、正確性と効率性が向上します。
- ■業務の標準化と可視化
- システムによる業務プロセスの標準化により、属人化を防ぎ、誰でも同じ品質の業務遂行が可能になります。また、各工程の可視化により、業務改善のポイントが明確になります。
生産管理システムの導入は、これらの課題を包括的に解決し、企業の生産性と競争力を大きく向上させる可能性があります。しかし、最大の効果を得るためには、自社の課題と目標を明確にし、適切なシステムを選択することが重要です。
なお、課題や業種、生産形態により適切な生産管理システムは異なります。以下のページでは、生産管理システムの特徴を比較しているため、製品選びの参考にしてください。
生産管理システム導入による改善事例
生産管理システムの導入でどのような課題を解決できるのでしょうか。ここでは、生産管理システムを導入した企業の事例を紹介します。自社の課題と照らしあわせて参考にしてください。
【改善事例1】棚卸し業務の効率化と決算処理の迅速化
金属精密切削加工を行う綾目精機株式会社様では、東証二部上場企業との経営統合を機に、生産管理システムの導入が必要となりました。それまでエクセルと台帳による管理を行っていた同社は、上場会社基準にあわせた四半期ごとの正確な棚卸しや、製品別原価管理の実現が課題でした。
生産管理システムの導入により、年4回の棚卸し作業時間が4日から1.5日に短縮され、月次決算に要する期間も半減しました。さらに、受注管理、出荷管理、外注管理、資材調達の発注管理などにもシステムの活用範囲を広げられました。
同社の取り組みで特筆すべきは、関係者全員で業務改善活動を行った点です。模造紙を使って業務フローを「見える化」し、システムでできることとできないことを明確化しました。この活動を通じて、従業員全員がシステムへの理解を深め、理想的な生産管理システムの実現に向けてモチベーションを高められました。
参考:導入事例:生産管理 TPiCS-X(綾目精機株式会社)|ITトレンド
【改善事例2】クラウド化による在庫最適化とパフォーマンス向上
配管・電設資材の製造販売などを手がける日栄インテック株式会社様では、事業の多角化にともない、複数の事業所間での情報伝達が非効率になっていました。また、拠点ごとに異なるシステムを使用していたため、集計作業に多くの時間を要していました。
生産管理システムの導入により、事業所間のペーパーレス化と入力業務の省力化を実現。さらに、原価把握や在庫管理が容易になり、適正在庫での運用も実現しました。その後、システムをクラウド環境に移行したことで、「ネットワークパフォーマンスの大幅な向上」「インフラ整備コストの削減」「バックアップ作業の簡素化と復旧時間の短縮」など、さらなる改善効果が得られました。
参考:導入事例:生産管理 R-PiCS V4(日栄インテック株式会社)|ITトレンド
【改善事例3】システム導入による製造ルールの徹底と納期遅れの解消
創業460年を超える老舗メーカーの株式会社ナベヤ様は、精密治具や治具システムなどを製造しています。同社では長年、手計算に頼った生産管理を行っており、既存のシステムでは所要量計算(MRP)の活用が困難な状況でした。
生産管理システムの導入により、MRPによる発注が可能となり、無駄な生産や発注漏れが解消。さらに、システムが原因の納期遅れがゼロになり、工程ごとの納期遅れも大幅に減少しました。また、基準在庫の設定が可能になり、在庫管理の最適化にも成功しています。
システム導入により、「製造ルールの徹底と工程の規則正しい流れの実現」「工程ごとの納期チェックの効率化」「基準在庫の設定による販売機会損失の防止」といった点が改善されています。
参考:導入事例:生産管理 TPiCS-X(株式会社ナベヤ)|ITトレンド
生産管理システムの導入で課題を解決しよう
生産管理業務には、さまざまな課題を抱える企業が多くあります。課題解決には、進捗状況の可視化や業務のマニュアル化、生産管理システムの導入がおすすめです。ミスの軽減や納期遅れをなくす、適正在庫などの事例をもとに、課題解決の参考にしてください。また、自社の課題にあった生産管理システムの導入を検討しましょう。
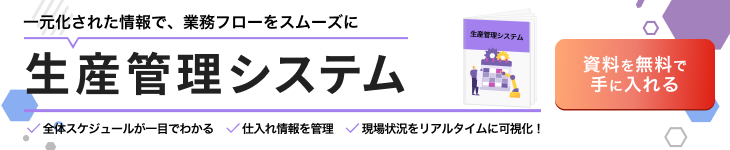